In recent years, with the decline of demographic dividends and the return of manufacturing industries in developed countries, the living space of traditional manufacturing industries in our country is facing a compressed situation, and the rigid increase in labor costs has constrained the development of most enterprises. In order to reduce the cost and increase efficiency, the government-driven and enterprise-driven "machine-for-man" tide is accelerating its deployment. Plants that are completely replaced by robots for manual manufacturing and processing are also emerging. In the process of manufacturing and processing, the process of loading and unloading is more people, and it is also the main link for machines to replace people. This paper introduces the case of fan housing manufacturing.
Introduction to the manufacturing process of the fan housing The automation of the manufacturing process before the automation: 8 manual completion of 9 sets of cumbersome processes, including inner ring spot welding, mesh cover hydroforming, outer ring touch welding, outer shell trimming, middle ring welding, outer ring circle, For the outer ring butt welding, middle ring knitting, middle ring butt welding and the like, the manufacturing process has the problem of high labor intensity but low efficiency. Fan housing manufacturing site map
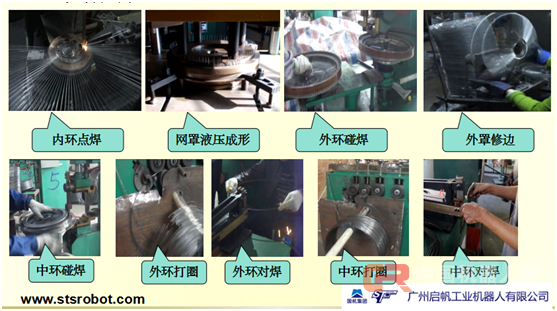
Overall layout design of automated production line (1) Analyze the process flow of the integrated machine tool; (2) Design the non-standard grasper at the end of the robot; (3) Design the auxiliary feeding positioning tool; (4) Calculate and analyze the appropriate robot; ( 5) Realize the communication between machine tool and robot. Overall layout of the production line 3D-LAYOUT
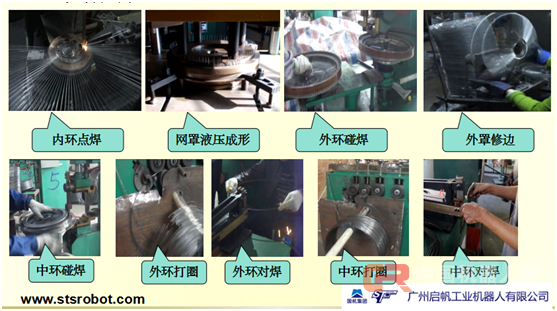
Overall layout of production line 2D-LAYOUT
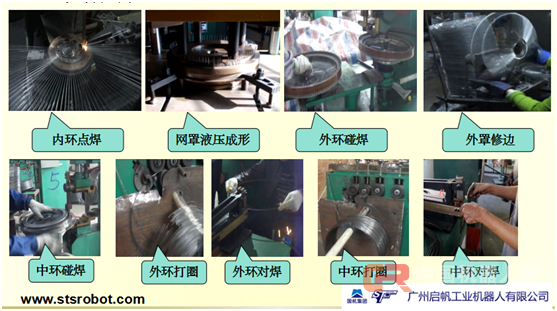
The effect of automation in production lines (1) Improves the stability and uniformity of product processing quality; (2) Improves production efficiency and can continue production for 24 hours a day; (3) Improve worker's labor intensity and improve safety; (4) Reduce The technical requirements of the workers. Kaifan Universal 6-Axis Robot Kaisha Universal 6-Axis Robot is a 6-joint robot developed and designed based on international industry standards. It consists of a robot body, a robot controller and a robot control software. The components are shown below.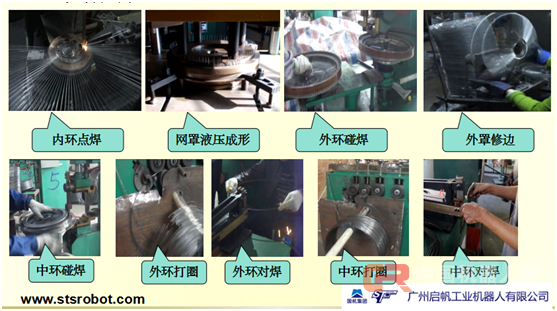
The control software was independently developed by Guangzhou Qifan, providing users with a fully open, scalable control system development platform. For different application research and development projects, users can easily add vision sensors, force sensors, infrared sensors, etc. to the control system, or extend the robot's functions by adding various end tools to fully realize industrial robots. Multiple applications. The three-dimensional robot simulation function is the unique highlight of the control system. By the method of first simulation and operation, the unexpected occurrence of the robot is effectively avoided. This case fully demonstrates the outstanding superiority of industrial robot loading and unloading in manufacturing and processing. It not only achieves the purpose of reducing costs and increasing efficiency, but also properly solves the problem of difficult recruitment for enterprises, and further expands the combination of organic robots and machine tools for industrial robots. The function of processing simplifies the operation mode of the machine tool, improves the operation safety of the machine tool, reduces the labor intensity of the workers, and greatly improves the work efficiency. It is an important part of the “black light factory†of manufacturing and processing, and has powerful applications. value.
Introduction to the manufacturing process of the fan housing The automation of the manufacturing process before the automation: 8 manual completion of 9 sets of cumbersome processes, including inner ring spot welding, mesh cover hydroforming, outer ring touch welding, outer shell trimming, middle ring welding, outer ring circle, For the outer ring butt welding, middle ring knitting, middle ring butt welding and the like, the manufacturing process has the problem of high labor intensity but low efficiency. Fan housing manufacturing site map
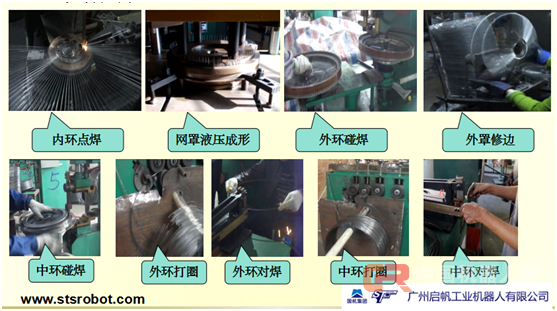
Overall layout design of automated production line (1) Analyze the process flow of the integrated machine tool; (2) Design the non-standard grasper at the end of the robot; (3) Design the auxiliary feeding positioning tool; (4) Calculate and analyze the appropriate robot; ( 5) Realize the communication between machine tool and robot. Overall layout of the production line 3D-LAYOUT
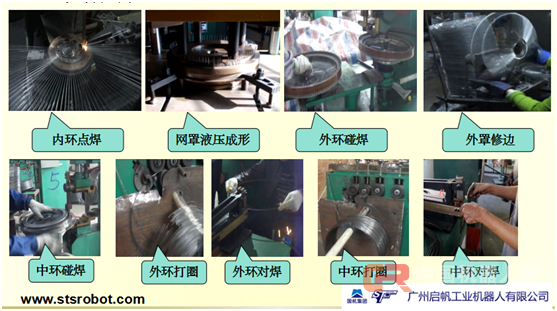
Overall layout of production line 2D-LAYOUT
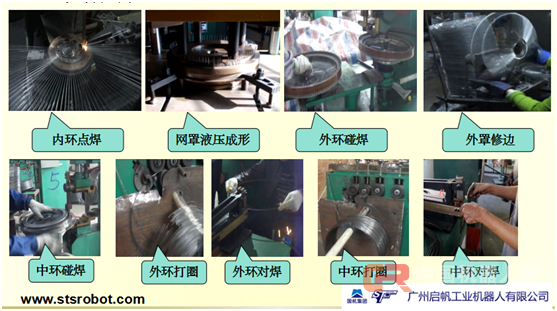
The effect of automation in production lines (1) Improves the stability and uniformity of product processing quality; (2) Improves production efficiency and can continue production for 24 hours a day; (3) Improve worker's labor intensity and improve safety; (4) Reduce The technical requirements of the workers. Kaifan Universal 6-Axis Robot Kaisha Universal 6-Axis Robot is a 6-joint robot developed and designed based on international industry standards. It consists of a robot body, a robot controller and a robot control software. The components are shown below.
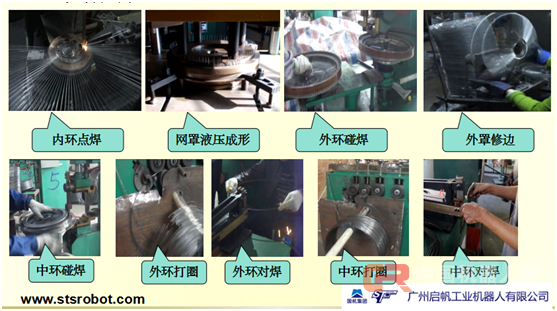
The control software was independently developed by Guangzhou Qifan, providing users with a fully open, scalable control system development platform. For different application research and development projects, users can easily add vision sensors, force sensors, infrared sensors, etc. to the control system, or extend the robot's functions by adding various end tools to fully realize industrial robots. Multiple applications. The three-dimensional robot simulation function is the unique highlight of the control system. By the method of first simulation and operation, the unexpected occurrence of the robot is effectively avoided. This case fully demonstrates the outstanding superiority of industrial robot loading and unloading in manufacturing and processing. It not only achieves the purpose of reducing costs and increasing efficiency, but also properly solves the problem of difficult recruitment for enterprises, and further expands the combination of organic robots and machine tools for industrial robots. The function of processing simplifies the operation mode of the machine tool, improves the operation safety of the machine tool, reduces the labor intensity of the workers, and greatly improves the work efficiency. It is an important part of the “black light factory†of manufacturing and processing, and has powerful applications. value.
Shenzhen Kaixuanye Technology Co., Ltd. , https://www.icoilne.com