O sensor technology is one of the signs of the development level of modern science and technology, and pressure sensor technology is an important branch of sensor technology. At present, various types of pressure sensors, such as diffused silicon, capacitive, silicon sapphire, ceramic thick film, metal strain electric type, etc., are being widely used in various industries and scientific and technological fields of national production. The following is a brief introduction to the characteristics of some common pressure sensors and their differences.
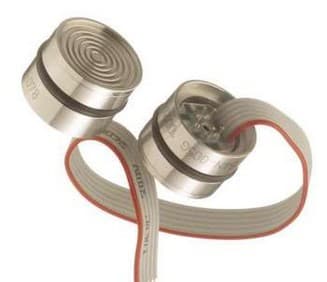
Sapphire pressure sensor
The sapphire pressure sensor uses the strain-resistance working principle and uses silicon-sapphire as the semiconductor sensitive element, which has unmatched measurement characteristics.
Sapphire is composed of single crystal insulator elements, which will not cause hysteresis, fatigue and creep phenomena; sapphire is stronger than silicon, has higher hardness and is not afraid of deformation; and sapphire has very good elasticity and insulation, so it is made of silicon-sapphire The semiconductor sensitive element is not sensitive to temperature changes, and it has very good operating characteristics even under high temperature conditions; sapphire has strong radiation resistance; in addition, the silicon-sapphire semiconductor sensitive element has no pn drift, so it is fundamentally simplified The manufacturing process is improved, the repeatability is improved, and a high yield is ensured.
Pressure sensors and transmitters made of silicon-sapphire semiconductor sensitive components can work normally under the harshest working conditions, and have high reliability, good accuracy, minimal temperature error, and high cost performance.
Diffusion silicon pressure sensor
The working principle of the diffused silicon pressure sensor is: the pressure of the measured medium directly acts on the diaphragm of the sensor (stainless steel or ceramic), causing the diaphragm to produce a micro-displacement proportional to the pressure of the medium, and the resistance value of the sensor changes. The electronic circuit detects this change and converts and outputs a standard measurement signal corresponding to this pressure.
Ceramic pressure sensor
The anti-corrosion ceramic pressure sensor has no liquid transmission. The pressure directly acts on the front surface of the ceramic diaphragm and the surface of the chamber diaphragm, causing a slight deformation of the diaphragm. The thick film resistor is printed on the back of the ceramic diaphragm and connected into a The Wheatstone bridge (closed bridge), due to the piezoresistive effect of the varistor, causes the bridge to generate a highly linear voltage signal proportional to the pressure and proportional to the excitation voltage. The standard signal is calibrated according to the different pressure ranges. 2.0, 3.0, 3.3mV, etc., compatible with strain sensors. Through laser calibration, the sensor has high temperature stability and time stability. The sensor comes with temperature compensation of 0 ℃ ~ 70 ℃, and can directly contact with most media.
Ceramic is a recognized material with high elasticity, corrosion resistance, wear resistance, impact resistance and vibration. The thermal stability of the ceramic and its thick film resistance can make its working temperature range up to -40 ℃ ~ 135 ℃, and has high precision and high stability of measurement. The electrical insulation degree is greater than 2KV, the output signal is strong, and the long-term stability is good. Ceramic sensors with high characteristics and low prices will be the development direction of pressure sensors. There is a trend to replace other types of sensors in Europe and the United States. In China, more and more users are using ceramic sensors to replace diffused silicon pressure sensors.
The advantages of ceramic thick film structure and force-sensitive Z-component complement each other
The thick film pressure sensor is another major technological innovation of the pressure sensor after the diffused silicon pressure sensor, and the force sensitive Z-component is currently the only sensitive component with digital signal output at home and abroad. Therefore, the ceramic thick film process and the force sensitive Z-component The clever combination of the simplest circuits of the components can lead to a new type of sensor with excellent performance and low cost. Specifically, the ceramic thick film process has the following advantages:
The ceramic elastomer has excellent performance, and the flat, uniform and dense materials strictly follow Hooke's law to the extent that there is no plastic deformation.
Thick film resistors (including high-temperature wires) can be sintered firmly with ceramic elastic diaphragms without the use of glue. This rigid structure has small creep, small drift, stable static performance and good dynamic performance.
The thick film elastomer has a simple structure and is easy to prepare. Compared with the diffused silicon pressure sensor, it does not require a semiconductor planar process to form a diffused resistance elastic diaphragm, which greatly reduces the initial investment and process cost of the production line.
The thick ceramic film structure is resistant to corrosion by liquid or gaseous media, and does not need to be converted and isolated by stainless steel diaphragms and silicone oil. The packaging structure is simplified, which further reduces costs.
Wide working range. The range is determined by the ratio of the effective radius of the diaphragm to the thickness. As long as the micro pressure is not less than 1Kpa, in principle, a higher range is also easy to achieve.
Wide operating temperature range, up to -40 ℃ ~ 120 ℃.
Structure Design of Ceramic Thick Film Force Digital Sensor
The ceramic thick film force digital sensor is mainly composed of three parts: a ceramic ring, a ceramic diaphragm and a ceramic cover plate. As a sensitive elastic body, ceramic diaphragm is made of 95% Al2O3 ceramic finishing, which requires flatness, uniformity and density. Its thickness and effective radius depend on the design range.
The ceramic ring is formed by hot die casting process at high temperature. A high-temperature glass paste is used between the ceramic diaphragm and the ceramic ring, which is fired together by thick film printing and thermal firing technology to form a peripheral cup-shaped inductive cup-shaped elastomer, that is, the ceramic cup-shaped fixed part should be formed Rigid structure without creep. On the upper surface of the ceramic diaphragm, that is, the bottom of the porcelain cup, the circuit of the sensor is made by thick film technology. The circular groove in the lower part of the ceramic cover plate forms a certain gap between the cover plate and the diaphragm. The limit can prevent the diaphragm from being broken due to excessive bending when overloaded, forming an anti-overload protection for the sensor.
Directly Supply Imported Stainless Steel Rod,SUS304 Imported Stainless Steel Rod, 316 Imported Stainless Steel Rod
ShenZhen Haofa Metal Precision Parts Technology Co., Ltd. , https://www.haofametal.com